Large machines. Large moulds. Large products.
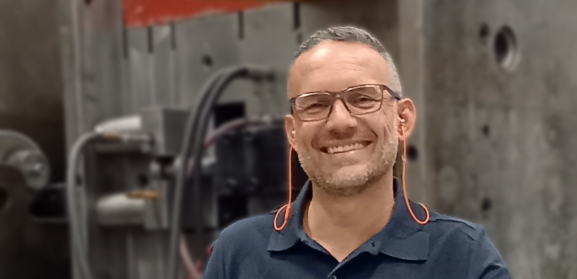
Injection molding of large products naturally requires the use of large molds and large machines. Injection molding remains the same process, but very large molds require some adjustments in the processes. The heaviest mold we work with weighs around 20,000 kg. You can't just set that aside or place it into a machine without preparations.
But then you get something impressive: we produce with molds up to 2.10 x 1.30 m, creating products weighing around 20 kg of plastic (*). And that's a nice challenge for José Coelho, our production manager. In this blog, he enjoyes talking about his work.
.
|
"I've been working in plastics for 20 years, but I've never encountered as many different, very specific plastics and machines as I have here," says José Coelho, who manages all our production departments, from Injection Molding to Assembly and Plastic Processing. "The variety of special plastics we use here is remarkable, but also the machine park with tonnages from 15 to as much as 2,100 is exceptional. Especially for a company in the Netherlands. The big machines are quite impressive. We've had a 1,500-ton machine for a while, the 2,100-ton machine has been with us since 2017, and since the merger of Pekago and Neaforma, we also have a 1,700-ton machine. Internally, we refer to them as 'our Big Seven': our seven largest machines." |
“Big” machine: big clamping force?"
Of course, no plastic should leak between the two parts of the mold. So: the higher the required force to inject the plastic into the cavity, the higher the needed clamping force to press the two parts of the mold together," José explains. "This is to prevent the plastic from leaking out of the sides. And these are truly significant forces: a clamping force of 2,100 tons can be compared to the pressure exerted by a stack of 2,100 mid-sized cars!" |
.
|
However, this does not mean that the machine with the highest tonnage can also produce the largest or heaviest plastic products. This also depends on the size of the machine's screw. The larger the diameter of the screw, the more plastic it can inject. The combination of the screw and the clamping force determines the maximum size and weight of the product that the machine can produce. José continues: “But injection molding is always a complex interplay of factors like the machine used and other parameters such as the temperature of the mold or the plastic to be injected. This is no different for large molds or large injection molding machines compared to smaller tools. Each mold here is unique." "Injection molding is always
|
![]() |
Many different plastics
“We work a lot for clients who have specific requirements for the plastics used, such as aircraft interior parts or housings for analytical devices in a laboratory. These special requirements can include resistance to chemicals or sunlight, scratch or fire resistance. Hence the large number of different plastics we use. We use everything from ABS and PP to Ultem or glass-filled materials.”
.. ![]() |
Large molds also for TFC (Thermoplastic Foam Molding)The cavity of a mold determines the shape of the product. The larger the cavity, the more pressure is needed to fill it completely with plastic. The shape of the cavity (and thus of the product) can also pose a challenge to press the plastic into the furthest corners. In addition to regular compact injection molding, we also work with TFC (Thermoplastic Foam Molding). “If our engineers design a mold based on customer requirements, we can always perform a mould flow analysis,” José continues. “With a special program, it predicts how the liquid plastic will flow in the mold cavity. The machine's force plays a major role in this.” |
Installing large molds
“Pekago makes many different products in small and medium-sized series. This means that every machine is used for various products; we don’t have machines that make the same product for weeks or months. After producing a series, the mold is removed from the machine, and the machine is prepared by our machine setters for another product. This is also labor-intensive: each time a different mold needs to be installed, and the process parameters need to be set up by our process engineers in combination with the machine. This makes our machine setters and process engineers highly versatile.”
Many kilograms
The molds we use are usually made of steel. José: “So even the mold for a small product quickly weighs tens of kilograms. You can’t just place it in an injection molding machine by hand; it’s always done with a crane.” For our large molds, it quickly involves hundreds and even thousands of kilograms, with the corresponding cranes for that.
Horizontal or vertical hoisting
Whether a mold is inserted vertically or horizontally into the machine also varies per combination. To hoist a mold vertically (from above) into the machine, you need a lot of space above the machine for the crane plus the mold. We don’t have that space above all machines. Then it is necessary for the machine to have a movable clamp. Each machine has four clamps, cylinders, which move the mold parts towards and away from each other. The mold has to fit between these. Often, one of the top clamps is movable and can be placed outside the machine using a hydraulic system. This gives space to hoist a mold horizontally into the machine.
![]() |
. The four cylinders of the clamps and the hydraulic system with which one of the top cylinders can be placed outside the machine. This creates space for placing a large mold. |
Even very large molds are installed completely and all at once
“With very large and heavy molds, it might seem easier to hoist the front and back in one by one,” José continues. “A major disadvantage of this is that the cavity (form) is then open and unprotected. A small collision of the cavity surfaces with something hard can cause irreparable damage. This damage will be visible in the plastic product. Therefore, despite the challenges of size and weight, we always choose to install the mold completely, all at once, into the machine.”
Safety is paramount
“Now that we’ve talked about the enormous weights of the molds, you can imagine that we have strict safety requirements for working with these molds.” José continues seriously: “An accident can happen easily but with these weights, it can have huge consequences. All our technical staff, such as machine setters and mold handlers, regularly attend courses to ensure safety is guaranteed. We are at least as careful with our colleagues as we are with our production equipment.”
. . . Do you want to know more about the possibilities for having large plastic products made by Pekago? |
|
Pekago’s production manager
José Coelho with some of the
large molds in production
at our facility
.
.
(*) The specific maximum (and minimum) sizes, weights and volumes depend on factors such as
the used injection moulding technique, material, machine, and design of the product.