Also true for the healthcare sector: 3D-printed products are there sooner, but injection moulding is quicker
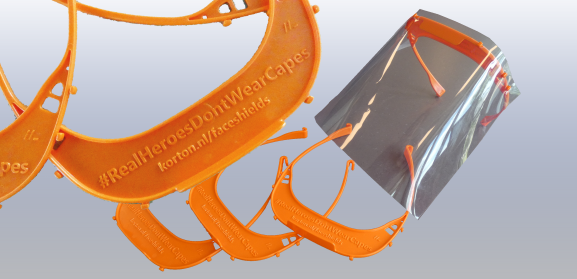
In recent months, face masks have allowed healthcare staff to work in close proximity to patients and inpatients in order to administer proper care and minimise the risk of infection. However, high demand has resulted in a shortage of face masks and many healthcare institutions were unable to get hold of them!
Until recently, Korton Group just supplied IT solutions to healthcare institutions. But because of the shortage of face masks, they decided, together with some partners, to expand and print masks with a 3D printer. Though they were quickly able to scale up production to 600 masks a week, which alleviated the initial need, the need turned out to be much greater than expected.
Someone yelled ‘injection moulding’… but they'd only vaguely heard of it. Fortunately, they found Pekago on the web, which could in any case investigate whether injection moulding could indeed offer a solution.
This was going to be an exciting project. Normally, making a mould takes so much time that investing in such a (hopefully!) short-term project makes little sense. But the volumes that could be manufactured per week with injection moulding would far exceed 3D printing.
Emergency knows no law
Yes, building a mould takes time. A lot of time. In fact, the entire process can take months. However, a good 3D file was available, the design was not too complicated and the mould cavity could be fully milled. Of course, we had to skip all kinds of steps: no difficult materials, no package of requirements and no optimisations. And with a bit of luck and, above all, genuine will and effort, we were able to achieve a capacity of about 8000 pieces per week within just a week and a half of the order! That's how we achieved something beautiful in a time of crisis.
Read more about 3D printing versus compact injection moulding.