In Kunststoff eingesetzte Teile – "mehr als nur ein Loch für ein Schräubchen"
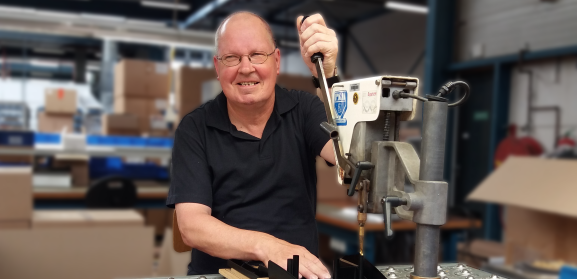
Jan Rijpert, schon seit 28 Jahren bei Pekago unser Experte für die Montage von Kunststoffteilen, lacht: „Einsatzteile entscheiden in der Tat oft über Gedeih und Verderb von Kunststofferzeugnissen.“ Je nach Funktion und Anforderungen an den künftigen Produkteinsatz, überlegt man schon in der Entwurfsphase, welcher Einsatzteiltyp für die Montage optimal ist.
Einsatzteile zur Montage von Kunststoffteilen“Die von Pekago hergestellten Kunststoffgehäuse und weiteren Produkte werden meistens auf andere Teile montiert. Zur Befestigung sind dann oft Einsatzteile nötig”, erzählt Jan weiter. “Schon bei der Produktentwicklung überlegen unsere Ingenieure und der Auftraggeber gemeinsam, welche Einsatzteile sich am besten einsetzen lassen.
Dabei betrachten sie u. a. die Wandstärke des Produktes, aber natürlich auch den Kunststoff, aus dem es gefertigt ist. Ein normales Einsatzteil kann bspw. ein TSG-Produkt völlig zerstören, weil der Thermospritzguss zu einem poröseren Material als bspw. ein normaler Spritzguss in ABS führt. Für TSG-Produkte nimmt man darum oft Einsatzteile, die mit dem Kunststoff verschmolzen werden. Bei Spritzguss haben wird grundsätzlich die größte Auswahl an Einsatzteilen“.
Welches Einsatzteil optimal ist, richtet sich auch nach der benötigten Zugkraft, die es auszuhalten gilt. Welchen Kräften muss das Produkt nach der Montage letztlich widerstehen? Wird es nur einmal montiert oder ggf. regelmäßig an- und abgeschraubt? Auch das stellt wieder andere Anforderungen an Material und Montage der Einsatzteile. Zum Einbringen der Einsatzteile in den Kunststoff wendet Pekago drei unterschiedliche Methoden an. „Für alle Einsatzteile berücksichtigen wir schon beim (Spritz-) Guss den benötigten Lochdurchmesser im Kunststoff, also die Aussparung für das Einsatzteil. Deren Größe richtet sich dann wiederum nach dem zu nutzenden Einsatzteil“, erklärt Jan.
Einsatzteile gibt es in vielen Größen und Materialen
Andere Befestigung, anderes Einsatzteil
Wie Jan verdeutlicht, wendet Pekago vorwiegend folgende drei Methoden zum Einbringen der Einsatzteile in den Kunststoff an: Eindrehen, Einschmelzen und Ultraschallschweißen. „Eindrehen ist, wie gesagt, für TSG-Produkte ungeeignet, ergibt in anderen Materialien jedoch die größte Zugkraft. Dabei nutzen wir Einsatzteile aus Edelstahl, Stahl und Messing. Beim Eindrehen wird das Einsatzteil ‘einfach’ in die Aussparung im Kunststoff gedreht. Weil das Einsatzteil etwas größer als der Lochdurchmesser ist, ‘schneidet’ das Gewinde außen am Einsatzteil selbst eine Nut in den Kunststoff.“
„Beim Einschmelzen führt man einen heißen Stift in die Mitte des Einsatzteils und erhitzt es so. Das Einsatzteil wiederum kommt in das Kunststoffmaterial und schmilzt es. Ein Schmelzeinsatzteil hat Rippen. Es verfestigt sich im Kunststoff, wenn man das Material abkühlen lässt. Einschmelzen dauert länger als Eindrehen, weil das Material zuerst erhitzt werden und dann wieder abkühlen muss. Das verteuert das Einfügen der Einsatzteile natürlich“.
Jan verdeutlicht: „Für TSG-Produkte wird fast immer das Einschmelzen gewählt. Bevor die Produkte Einsatzteile erhalten können, müssen sie 24 bis 36 Stunden ausschrumpfen und verdampfen. Der Kunststoff gelangt schließlich flüssig (sprich: heiß) in die Spritzgussmaschine und schrumpft dann beim Abkühlen, indem die entstandenen Gase aus dem Kunststoff entweichen. Würden die Einsatzteile sich beim Ausschrumpfen bereits im Kunststoff befinden, so könnte das Produkt sehr schnell an den Einsatzteilen reißen. Die lange Abkühlzeit, die vor dem Einschmelzen des Einsatzteils nötig ist, verlängert selbstverständlich die Produktionsdauer“.
“Wenn der Kunststoff zum Schmelzen zu hitzebeständig ist, wird die Methode Ultraschallschweißen angewendet. Dabei wird das Kunststofferzeugnis in eine speziell für dieses Produkt entwickelte Form gelegt. Jedes Produkt benötigt eine eigene Form, weil es genau darauf ankommt, wie die Einsatzteile platziert werden. Unter dem Schweißgerät wird das Einsatzteil manuell an die richtige Stelle gesetzt. Danach kommt der Stempel des Ultraschallschweißgerätes auf die Einsatzteile und das Produkt. Hochfrequenz-Ultraschallschwingungen verankern das Einsatzteil im Kunststofferzeugnis. Auch diese Einsatzteile haben Rippen. Ultraschallschweißen sorgt für die schnellste Montage, mit der benötigten Form sind jedoch zusätzliche Kosten verbunden. Die Formen werden per 3D-Druck gewonnen oder aus Aluminium gefräst. Außerdem ist das Ultraschallschweißen sehr laut! Deshalb geschieht es in einem separaten Raum und stets mit Gehörschutz“, so Jan.
Entscheidend ist auch das Material der Einsatzteile
Auch das Material der Einsatzteile ist zu beachten, und die Wahl richtet sich nach der gewünschten Montageart und den Nutzungsanforderungen. “Pekago arbeitet hauptsächlich mit Einsatzteilen aus Edelstahl und Messing. Messing leitet Wärme viel besser als Edelstahl. Deshalb erhitzt sich ein Einsatzteil aus Messing schneller, und erfolgt auch das Einschmelzen zügiger. Edelstahl wird natürlich häufig gewählt, wenn das Endprodukt mit Feuchtigkeit in Berührung kommt. Bevor wir Edelstahleinsatzteile einschmelzen, erhitzen wir sie oft zunächst mit einer Warmhalteplatte. Dann haben wir sozusagen kalten Kaffee!
So gibt es beim Einfügen von Einsatzteilen in Kunststoff allerhand zu beachten! Doch das tun wir schon sehr lange und nahezu ständig. Uns überrascht so schnell nichts mehr”.
Können Einsatzteile auch Ihren Kunststofferzeugnissen eine bessere Befestigung bieten?
Das untersuchen wir gerne zusammen mit Ihnen. Rufen Sie uns an, um einen Termin zu vereinbaren: 0031 13 5308077.