Coating plastics: optimum result due to integrated approach
Those who think that plastic products can be coated ‘just like that’ can be very disappointed with the results: surface faults such as flow lines, marks and spots are all too common.
Housings for equipment such as measuring and analytical devices are frequently made of plastic. There are various technologies available to this end, including compact injection moulding and structural foam moulding (SFM for short). SFM is a form of injection moulding in which, by the addition of a foaming agent, very robust and visually attractive plastic components can be manufactured. These often form interesting alternatives to metal housings and frames.
1
Equipment used in hospitals and laboratories has to be resistant to chemical cleaning materials. It has to withstand knocks and bumps and is, of course, expected to have a high quality appearance. In outdoor applications, such as toll checking systems and parking terminals (see the photo above), the housings in question are exposed to every kind of weather: hail, snow, ice and ultra violet radiation. Finally, many devices must also meet requirements in the areas of fire safety or electronic shielding.
1
The optimum combination of a plastic housing with a suitable coating system is needed if all these requirements are to be met. It is not sufficient for both technologies to excel in their own rights. The two technologies have to be tailored to suit one another. After all, the product that comes out of the injection moulding machine (the plastic component) is the direct input for the coating process.
1
It is sometimes thought that any imperfections which have arisen during the injection moulding process can be camouflaged during coating, but this is only partly true. If, however, the finishing is taken into account during the design and making of the plastic component, the high costs of (manual) reworking afterwards can be avoided.
1
Before the coating can be started, the plastic component must be pre-treated in accordance with the client’s requirements. Seams and sprue or gate marks can, for example, be ground down and sink marks can be remedied by filling. This pre-treatment requires expertise, is labour intensive and is, therefore, relatively expensive.
1
Designing coated SFM housing
Attention paid to the finish earns itself back
Expensive manual work can be obviated by taking the surface requirements into account in the design phase. The following tips may be useful here:
1
- Choose the right plastic. There are a great many plastics available, which makes it difficult to determine the most appropriate one for the product in question. Firstly, the material must meet the requirements laid down in terms of rigidity, dimensions, fire and UV resistance and so on. It is also advisable to incorporate ‘coatability' in this choice. Polyamide, polyethylene and polypropylene, for instance, are materials which must have a special (and therefore relatively expensive) pre-treatment. Substances which are added to the plastic to influence its properties (such as glass and talcum) may affect the coatability of the plastic component, too.
- Ensure that SFM products have the optimum wall thickness. Although the use of foam does indeed decrease the likelihood of sinks, a better wall thickness ratio reduces the cycle time and results in fewer stresses in the product.
- 'Equal = not equal'. If two components, such as the bottom and top of a housing, are assembled together, or a housing is composed of multiple components, seams will inevitably be visible between the various parts. If this is the case, a great deal of effort will be needed to achieve an acceptable appearance. The simplest solution for this is to allow the various parts to overlap slightly, thus producing a shadow along the edge, but ‘clever’ mould parts can also help.
Two SFM components glued together without a ‘shadow edge’: a good result after a lot of manual work. The product is a housing for a toll checking system.
- If a component is to be coated in two colours, the interface between them is always the subject of discussion. A clear transition in the product geometry, that is, which is already clear in the plastic part, is helpful in this case. The high costs resulting from masking work can thus be avoided.
- Furthermore, the integration of suspension points and the spray mist must also be taken into account when designing the product.
Moulds
Coating vital aspect in the development of production tools
Besides the aspects which have a direct effect on the product design, matters such as the mould construction, cooling and type and position of injection point are of great importance. A well-chosen position for the injection point and runners can prevent undesirable swirling, flow disturbances and sinks. The fewer the injection moulding-related technical problems, the easier it will be to coat the product.
1
The last fine tuning can take place during the trial spraying. Often the shortest possible cycle time is opted for so that the component can be delivered as cheaply as possible. The consequence is that the coating mechanic has to deal with a more laborious product than strictly necessary. Sometimes it is advisable to allow the component to foam for rather longer in the mould or to operate the injection process slightly differently. This is always cheaper than having to grind or fill imperfections manually afterwards.
1
Click here if you want to know more about designing moulds for SFM.
1
Choice of a coating system
Coating and primer are essential aspects of the processing time and quality
The correct choice of coatings and primers is an art in itself. There is ample choice when it comes to coating systems and the most expensive is not necessarily the best. Important points to consider when choosing a coating system are as follows:
1
- What is the material to be coated? What plastic will be used and what fillers (such as glass) or foaming agents are envisaged?
- What is the desired effect? Does the client want a ‘splashed effect’ or a coarse or fine structure? The various possibilities all have a specific effect on the price. Some coatings partly ‘disguise' surface faults on the plastic component but require a longer coating time.
- The application: indoors or outdoors, chemical resistance, hygiene requirements, cleanability of the surface.
Click here if you want to know more about various coating possibilities, including electromagnetic Compatibility (EMC) coating and coating effects.
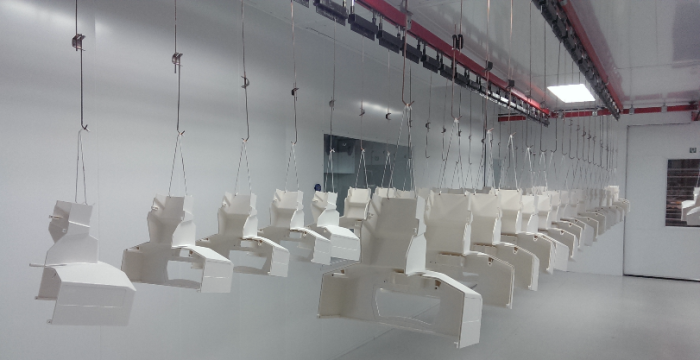
Liquid spray coating in a professional paint shop.
1
In conclusion
The production of plastic SFM housings and the coating of plastics are both distinct areas of expertise. But substantial gains can be achieved in terms of quality, costs and lead times if the right choices are made in the development phase and the two technologies are well harmonised with one another. If a supplier has both technologies under a single roof, the risk of making the wrong choices in the preliminary stage is minimised and expensive mistakes in the execution can be avoided.