Spuitgieten, TSG, lakken en assembleren van uw kunststof behuizingen en technische componenten
Moulds from China: not just cheaper
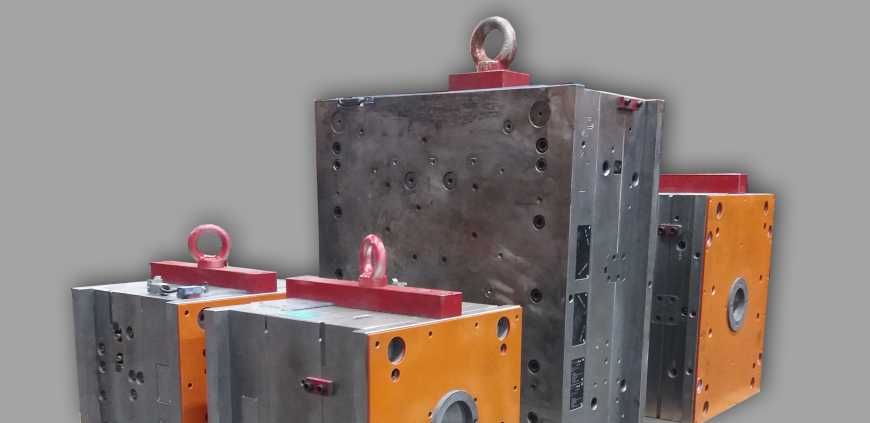
"Of course moulds from China are cheaper, but that's not the main reason why we buy them there. It may sound strange, but I can get things done faster on the other side of the world than in Europe."
Wil Mathijssen is jointly responsible for purchasing and technical evaluation of moulds at Pekago, and he deliberately does this in China.
"If I find something wrong with a mold in China, it's adjusted the next day. It doesn't matter if it's 6 a.m.: they get it done because it's in their interest. Sometimes I wish we had the same work ethic in Europe. I don't go home until the work is done. That's why I feel comfortable with this way of working."
Do you travel to China often?
"I travel to China an average of three times a year, typically for two weeks per visit. We oversee the design and production of a mould from the Netherlands, and usually let the Chinese handle the initial tests themselves. They are also getting better at reporting how they produced. They then send a test product and photos of the mold and conditions. We review these with the entire team, including different disciplines like project management. We evaluate the test product and discuss everything with the customer. All final comments are incorporated, and when it's ready, we fly to China. We try to cluster work for multiple clients so we don't have to fly back and forth for a single mold."
"When we're there, we do the 'acceptance': checking and running tests with our plastics and under our conditions. They need to fix anything that isn't right; the mold must work well before I return. If not, we extend the stay, but fortunately, that doesn't happen often."
(The text continues below the photo)
Wil and engineer Patrick inspect a newly completed mold in China
And then the mould can come to the Netherlands?
"Exactly. Sometimes customers want the initial production in China to save time, but ideally, we prefer to do it here at Pekago. The mold goes into a crate and is transported by plane, train, or boat, depending on how quickly we need it here. Before transport, the mold is injected with wax and vacuum-packed to protect it from extreme weather conditions. Once in the Netherlands, it's unpacked from the crate and bag."
"I don't have any work left once it's here: the mold manager performs checks to ensure all changes have been made. Then the mold is cleaned from te wax and set on the machine with the same parameters as in China. After a 'process release,' it can start working. Very rarely does something go wrong with the mold, but there's always a warranty. We ask the Chinese for the same warranty we offer our customers; it should last a certain amount of time without significant costs."
(The text continues below the photo)
The performance of the mold is carefully monitored
Who do you work with in China?
"We work with three to four suppliers in China. Each has their own specialties; some are better with precision molds, others with high-temperature molds. That's a different segment, made from different types of steel with different tolerances. Some suppliers are better with smaller runs and larger molds, while others handle larger quantities."
"We try to cluster visits to suppliers as much as possible, but it depends on their locations. Fortunately, they are all within about two hours' drive of each other. Usually, we're picked up and dropped off by the suppliers' employees. I don't drive in China; it seems better for everyone, haha! They usually have to pick me up and drop me off at the hotel, not at a competitor's," Wil laughs. "I certainly don't dislike my visits to China, aside from the long flights. My Chinese isn't that good, but that's not necessary. There's quite a bit of English spoken in China; we're not really in the hinterlands. They're hard workers, and I can work well with them."
Would you like to know more about purchasing molds in China or have other questions for Wil Mathijssen? Feel free to email or call (0031 13-5348434); he's happy to help.
« Back